Less is more
Press release - 18.06.2021
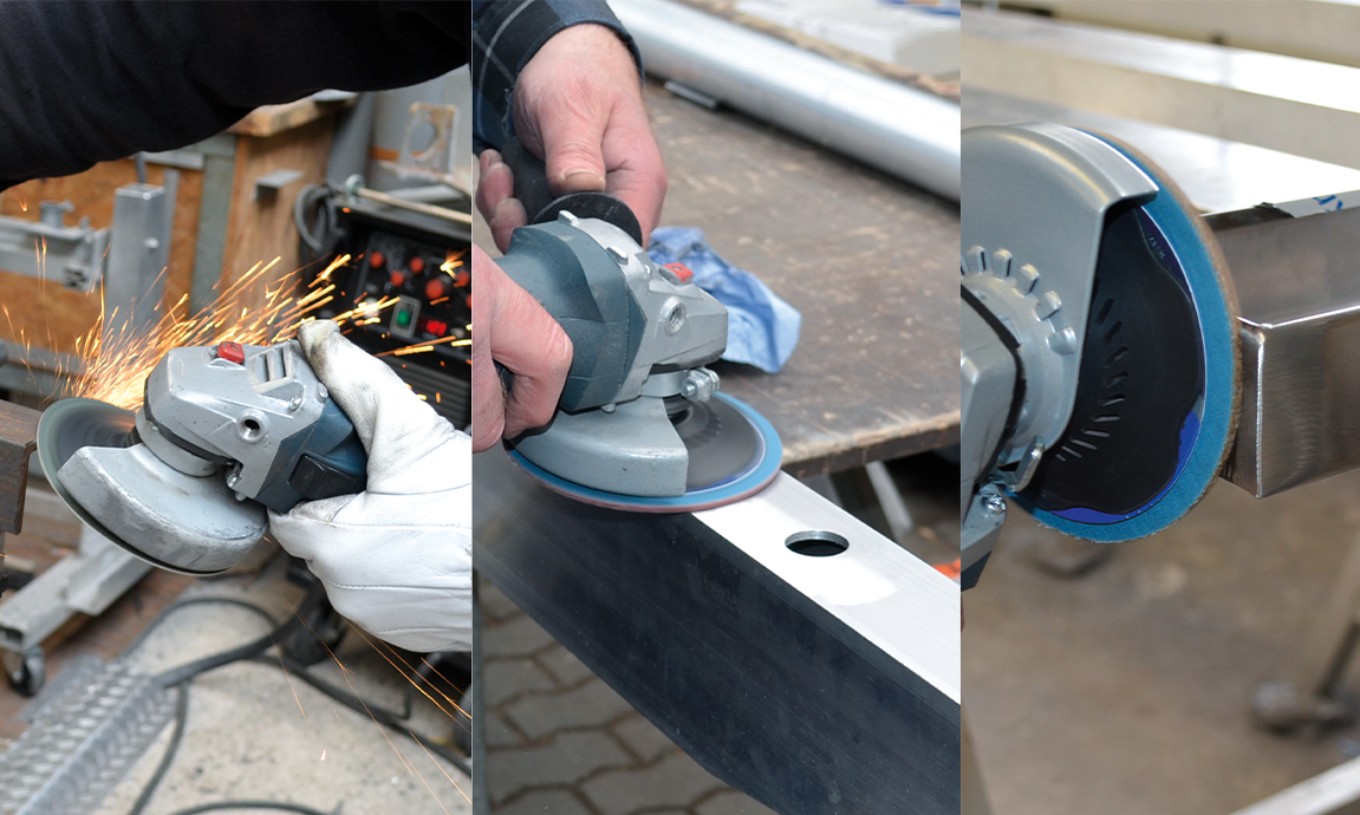
Less is more does not necessarily apply at Werhand in Neuwied, as Werhand is organized in line with its customers’ wishes. Master Mechanic Jörg Hörter has nevertheless been successful at creating more with less. He significantly reduced the number of tools used for everything from coarse grinding to polishing in order to save time and money.
The tradesmen who come to Werhand in Neuwied can be certain that their wishes will be fulfilled. The company offers a broad spectrum of services that encompass roofing and plumbing work, sanitary and bathroom planning, electrical installation, heating installation, sprinkler systems, products and service in the field of alternative energy, and classical metalwork and locksmith work. The company tagline, ‘We are there for our customers – perhaps more than typical of other companies’, obviously doesn’t promise too much.
The company that is currently a family-run operation in the third generation was established in 1939. A total of 110 employees, including an engineer, 13 master craftsmen, two technicians, and 20 apprentices, represent the expert performance of many construction-related trades.
The company located in Rhineland-Palatinate has a broad customer base, proof of general satisfaction supported by its consistent focus on cost savings and economic efficiency alongside the wide range of services.
‘Here, each of us is challenged to find the best possible solution for our customers,’ confirmed Jörg Hörter, head of the family-run company’s metal workshop. His area’s main services include the production of railings and staircase and balcony systems, and many things that the other areas of the company require for construction sites. ‘Our strength is customization,’ said Hörter, pointing out that everything is produced according to customer requirements and a quantity of 1 is no problem. ‘In that respect, we are completely flexible.’
Alongside private building owners, many of the customers are other building trades, industrial companies, and municipalities. Steel, stainless steel, and aluminium are the primary materials.
Weld seam preparation and post-processing, and work on surfaces from coarse grinding to polishing are the focal points of the processes in his workshop: ‘We grind a lot and underwent a complete realignment in that area five years ago. We simply used too many tools. As a result, our deployment, procurement, and warehousing processes were complex and time-consuming.’ Together with the regional PFERD representative, the company streamlined its processes, moving from grinding wheels and flap discs to the COMBICLICK system from PFERD.
‘Back then, we usually began processing with the grinding wheel. Next, we removed the grinding wheel from the angle grinder and clamped on a flap disc. Then we removed the flap disc and put on a Velcro backing pad. And then we had two additional operations with fleece discs with different abrasive grains,’ said Jörg Hörter to explain what the typical steps in a grinding process used to be. ‘Today, we clamp the COMBICLICK backing pad to the angle grinder, use the CO ceramic oxide grain fibre disc in grit size 120, and then the POLIVLIES grinding disc – without having to remove the COMBICLICK backing pad. Done.’
With the change, Hörter added, they are not only able to save on many tools, but also save the time related to tool changeover: ‘Even if a changeover takes only 20 seconds – in my workshop there are 15 people, eight of whom regularly work with the angle grinder. Changeover time quickly adds up over days, weeks, months, and years.’ With PFERD, the company is now able to tap that huge reserve of productivity.
However, the workshop head who is also a welding expert did admit that the changeover wasn’t all that easy. ‘Initially, my colleagues weren’t necessarily convinced that a fibre disc could replace a grinding wheel, for example.’ After the first test, they quickly accepted the new solution – after all, they could work faster and more conveniently. ‘The colleagues liked the fact that the COMBICLICK tools have considerable less vibration than grinding wheels. Many of them thought that was quite pleasant,’ recalled Hörter.‘And the discs didn’t raise as much dust during grinding so the colleagues kept cleaner.’
Practical advantages also made the switch easier: ‘COMBICLICK doesn’t have a central clamping nut for fastening the grinding material. It uses a rear-mounted quick-mounting system instead. That makes very flat use possible, and I can avoid grinding scores, pocks or waves into the workpiece.’ COMBICLICK also keeps cool when in use, which prevents delays and protects the grinding tool against overheating, according to Hörter. That extends the tools’ service life.
‘When someone asks me what COMBICLICK tools are suitable for, I always answer “For everything”, as the system covers all work from coarse grinding to polishing. Taking all that into consideration and the fact that the grinding discs are really very effective, we save material, processing steps, and time with COMBICLICK. And the processing quality is excellent. Here, less is truly more!’